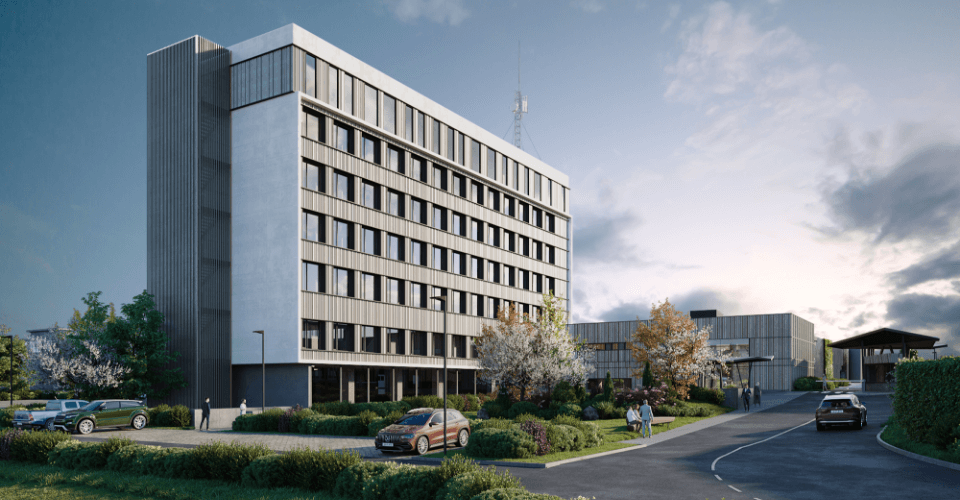
An energy self-sufficient industrial complex is being built in Tachov
Prague, 1st of June 2023 – The Urbanity real estate group has long been dedicated to building next-generation industrial
campuses.
Urbanity is currently developing an industrial park in the Tachov region. What stage is it in now?
Our goal is to create a next-generation industrial park. We create campuses close to people where production is the main
use, but accompanying services are very important, as they increase the comfort of the users, the employees of the campus.
This includes the possibility of putting a child in a preschool, the offer of quality meals, a mini-market, doctor, fitness
centre, accommodation capacity, etc. We want to create sustainable places where the employee comes preferably by public transport,
by bike or on foot and is able to spend some quality time here, even an hour before going to work or even after working hours.
So, we try to make sure that the employee does not have to drive to a remote area outside the town, somewhere in between some
fields, without facilities.
So, it is not a classic industrial complex, but has a slightly different concept...
Exactly. Even though the campus is focused on manufacturing companies, it primarily focuses on a quality working environment
and services for employees. Unlike traditional industrial or logistics centres, our campuses operate on a completely different
principle. We see the employees who work on campus and spend a substantial part of their lives here as our long-term and end
customers.
The complex in Tachov is not the only one you have under construction, but you also have other projects under development.
Which ones?
We have similar projects in Bruntal and Žirovnice. These are all brownfields where we are revitalising the existing buildings
and which we are also adding new buildings to. Another common element of our campuses is the fact that they are urban or suburban
complexes. In a way, this determines their use, because they are more suitable for manufacturing companies because of their
proximity to people than for logistics operations that employ a significantly smaller number of workers.
Let’s go back to the Urbanity Campus Tachov project. What was it originally used for?
The history of operation dates back to 1967, when the production complex of the national enterprise Plastimat was established
here. At that time, it was something like a showcase for socialist industry. The company produced various plastic products
for everyday life, had its own development and designed a wide range of products with a high aesthetic level. Then privatisation
came along, followed by the gradual decline of this production site. When we bought the complex, it was extremely under-invested,
energy-inefficient and partly abandoned.
So, you had to decide what to do next?
It was not a typical abandoned brownfield, but limited production facilities with a fifty-year history were still operating
here, employing hundreds of local employees. Our clear strategy from the beginning was to revitalise the existing buildings
in order to preserve the local identity, local production and employment, despite the fact that many other developers would
try to make a brownfield a greenfield because it is subsequently easier, and the construction is faster, cheaper and less
risky. We decided to completely revitalise the buildings, including the related campus infrastructure – and under full operation.
That must have been difficult...
We completely reconstructed the roofs and skylights, insulated the façades, replaced the windows, installed LED lighting,
changed the wiring, installed new heating sources with recuperation, added smart systems and modernised the facilities for
employees. All this without interrupting the operation of precise production susceptible to dust, humidity and temperature
changes. It really was a huge challenge.
So, there are three original buildings left?
Yes, they are buildings in the middle of the campus, today going under the names Alfa, Beta and Multifunction. Even though
they were completed in 1969, we managed to finish the comprehensive revitalisation of both original production buildings last
year with subsequent reconstruction. Their energy signatures are on level A, making them extremely economical. The rating
is somewhere around 10–15 points, which is very good. If there were no production facilities in the buildings, but only
logistics, for example, which is not as energy-intensive, it would be easier to evaluate and it could be said that energy
performance of the buildings is close to passive buildings.
Other buildings can be seen on the visualisation.
These include four more production buildings, the first of which was the Gama building, which we completed last year. We
expect the building permit to be issued in the near future for the others – Delta, Eta and Sigma. We are using the construction
lots that the production campus offers for the new construction, so we are complementing the existing buildings and not building
unnecessarily on fertile land.
Does this mean that you are creating a new, more modern form of the complex?
Yes, the complex will definitely be more modern, more sustainable, fulfilling the conditions of Industry 4.0, but I have
an interesting story about just how new it will be. After our urban planners designed a new building plan for the complex,
we ran across the original plan in the archive. And we essentially found out that what we drew was very similar to the original
design from 1953. This shows that the production complex is very well established and its further development has been well
thought out from the very beginning. In fact, we are just building on its history and continuing its story.
You do not build speculatively. What, then, is the occupancy?
Everything we have available today has been 100% leased for the long term. As for the other planned buildings, we are in
contact with several potential interested parties for whom we will customise the construction. By focusing exclusively on
manufacturing companies, we conclude contracts for ten or more years, which allows us to tailor the building and premises
to the client according to its requirements.
You have received several awards for this project. Can you mention them?
We consider the greatest success to be getting the prestigious international BREEAM Communities rating, being the first project
in the Czech Republic to do so. It is also the first municipal district in the world with a predominantly manufacturing function.
This certification is intended for larger sustainable parts of cities and public spaces, where there are more diverse buildings.
The certification confirms that the project creates a sustainable ecosystem with a clearly beneficial effect on the community
and the surrounding area. It contributes positively and thoughtfully to the urban, economic and social development of the
entire locality and extends the local civic amenities and transport and technical infrastructure.
Getting BREEAM Communities certification in the production complex segment must be quite challenging…
Definitely, because there are many more criteria to be assessed and in a much broader context. So, it is more time-consuming
and, of course, more financially demanding than other certifications. But it underscores what we are trying to create, a new
product, a next-generation industrial park. It is focused on community, sustainability, i.e., generally on a sustainable future
and the related prosperity. A lot more communication about the project is necessary as part of BREEAM Communities. Whether
with neighbours, citizens, authorities, institutions or the political representation. So, there is a great emphasis on ensuring
that all participants have the opportunity to comment on the project and be part of the decision-making process.
How does that work, exactly?
We presented the project in the affected municipalities and settlements, in public discussions, in the secondary technical
school, which we support, of course at councils and local authorities and at various associations and organisations, and we
are also planning on presenting the current development of the project in the retirement home and to the general public. Our
goal is to make as many citizens as possible familiar with the development of the site, everyone ranging in age from young
students to seniors. It is time-consuming, but on the other hand, our plan is essentially permanent, so it pays off in the
long run. We can see this ourselves in our relationships with the local community, which perceives us differently and in many
ways presents us to others as a positive role model, which is not a bad result for a Prague investor in the region.
What about the burning issue of energy?
In terms of energy self-sufficiency, last year, which was a ground-breaking year for us, we began the construction of the
largest roof solar power plant with a total output of over 5 GWh, which complements the sustainability of our complex. Together
with this, we are creating a unique decentralised community energy block within the Czech Republic, where we supplement the
roof power plant with 1.4 MW of battery storage and charging stations for electric vehicles. We are also gradually installing
heat pumps for hot water and heating in all the plants.
What about water?
We are very much dedicated to this throughout the entire spectrum. For example, in terms of drinking water, we have obtained
a building permit for our own wells and we are ready to provide a drinking water supply from 80-100% of our own resources.
The exact number will depend on the actual yield of the wells and the final form of the campus. We also manage rainwater,
we have implemented retention tanks, sills and detention basins for the gradual permeation of water back into the local landscape.
We have completed a project on the management of grey water. So, from this point of view, I think we are implementing a wide
range of applications beneficial to nature and to the users of the complex and its sustainability.
So, the goal is the highest degree of self-sufficiency?
There is currently a long-term measurement of the intensity, direction and type of wind in the campus in order to choose
the best installation of the planned wind power plant in the form of vertical turbines, thus obtaining another source of RES.
We have also developed a medium-term hydrogen strategy that we would like to pursue intensively over the next three years.
Of course, in the case of energy-intensive production plants, achieving complete self-sufficiency is difficult. But we like
a good challenge in Urbanity.
The campus will also include accommodation facilities. What can you tell us about them?
It is one of the wide range of services that increase the comfort of people who use the campus but are also intended for
the general public. There is an original 50-year-old office building in the complex, which we are currently converting into
a multifunctional building. About 60% of it will be used for hotel-style accommodation. In the remaining part, there will
be services such as a restaurant, an occupational doctor and dentist, specified areas for a children's group, fitness centre,
community room, café, mini-market and other supporting services. The advantage of this building is that it is located in
front of the entrance to the campus, so it is freely accessible to the wider community.
What other plans do you have here?
We are also preparing residential construction here, villas with start-up apartments, and a full-fledged preschool for 48
children. This again represents a strengthening of the urban social infrastructure, which the town naturally welcomes. We
are responding to a nationwide problem, where there are no available flats or room in preschools. In Tachov specifically,
more than 60 children were not placed as of September 1st of last year. Once again, this is conceived as a service not only
for the local employees, but primarily for the entire community. Our goals are to fulfil the principles of the city of short
distances concept, whether by offering our own services and functions directly on campus, or accessible within a 15-minute
walk or bike ride for the whole town and community. Clients, employers, strongly perceive the need to be where people are
and to not expect people to have to commute long and hard to get to them, which has a significant positive impact on reducing
carbon emissions in the town and its surroundings, as well as dust and noise from personal transport, thus improving the quality
of life.
Arnošt Wagner
Photo: Urbanity Archive