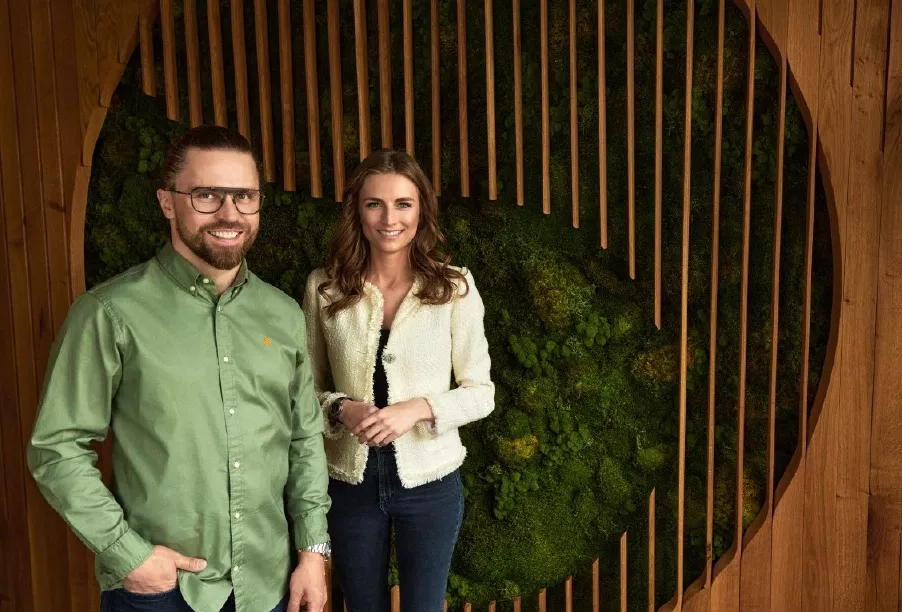
A new generation of industrial complexes is going up in Czech Republic
You’re currently preparing and building three industrial campuses – in Tachov, Bruntál and Žirovnice, which you are trying to approach in an innovative way. What do you think industrial construction of the future should look like?
Roland Hofman: We’re focusing on the needs and quality of the working part of the employees’ day. We're creating an attractive place to work. It is not only about their own space for the production and employees’ facilities, but also about the follow-up services so that the employee can spend some good quality time on the campus, an hour before or an hour after work, for example. Maybe he could accompany his child to the preschool that is directly on the campus, work out in the local fitness centre, shop at the minimarket, or go with colleagues after work to a café.
This approach is already quite common in office complexes. Will this also be a new trend in industrial areas?
RH: This is a unique approach in the industry right now. We want to show that even in this segment it can be successfully applied. After all, people don't only work in offices, so even industrial buildings deserve a high-quality environment, including related services. In recent decades, these grey boxes have been created in the vast majority of greenfields, which I personally consider to be the dark ages of industrial architecture. Therefore, we take a high-standard approach to our campuses from the point of view of architecture, whether in urban design, the design of façades and furniture, or landscaping. We choose Czech architects to design unique solutions for our projects, and we give them a relatively free rein. The campus in Tachov was prepared by the Komplits studio from Olomouc. The one in Bruntál was designed by the studio JA Architekti.
Markéta Šimáčková: We want people living in the regions to which we are coming, to see us as long-term and responsible partners because they will know that we will be bringing new services and aesthetic solutions that are a perfect fit for their town.
Did you come up with this concept yourself, or are companies looking for new spaces for their production?
RH: We’re creating a new product. The lack of a skilled workforce is one of the major issues that industrial firms must address. When we create attractive campuses, we help our tenants in becoming preferred employers in the given location. So, we also secondarily deal with their personnel issues. When a company newly comes to a region, it does not have to complicatedly find and convince employees. Through us, it offers them a job in an environment that they won’t find elsewhere.
What will they find in your buildings compared to other industrial complexes?
RH: The overall design of the campus is of a higher standard. A wide range of support services are available on site to enhance the comfort of users or visitors to the campus. Another important aspect is that our campuses are part of the city. Employees can walk to work. In Tachov, it is about a kilometre from the main square. In Bruntál, we are 300 metres from the train and a bus station.
MŠ: It isn’t common for industrial buildings to pay such close attention to architectural aspects in interiors. We’re also trying to change that. A high-quality environment also has a positive effect on the employees. We have prepared four sample visuals for the interior, prepared by the architect and designer. In each, the colours and materials are coordinated. We’re not just building classic white plasterboard inhall units.
Are the tenants willing to pay higher rent for the deluxe design?
MŠ: The companies in our campuses pay market rent for a building they have customised to their needs. The other features on the campus that contribute to the overall comfort, including a greater intensity of greenery, are not factored into the rent. The same applies to the associated services. Also, the operators of these services know that there is a high enough concentration of people on the campus and its surroundings to use the services.
Even so, your concept for the construction must be more expensive than for standard projects.
RH: It’s definitely more time-consuming because everything is customised and has elaborate details. Financially, our approach is more expensive, but because we’re not a classic developer who needs to build and sell quickly, we can afford it. We’re an investor who has a permanent vision in all the locations. We have no time limit for when we would have to withdraw from the investment and sell the campuses. This approach gives us more freedom to invest much more energy and effort into projects. Thus, we’re able to focus much more closely on the long-term sustainability of our projects.
But you still need to monitor the return on your investments.
RH: Of course, though we have set parameters and timeframes for the return that differ from standard projects. And it works out for us. The higher initial investments also return in different ways than in purely financial terms. We know that we can fill up the premises more easily, faster and with longer rental periods, because they are more interesting and of a better quality.
MŠ: It isn’t easy for our tenants to leave us. It would be hard to explain to their employees that they will be moving elsewhere, away from such a unique place.
Will the services on campus be available to the wider public than just the employees of companies that are leasing from you?
MŠ: The services are accessible to the general community, which fully fits into our vision. At the Tachov campus, most of the services take place in a multifunctional building, which is right at the entrance to the campus.
RH: We’re not in a field on the outskirts of town where people would have to drive to get to us. On the contrary, we’re an integral part of the city, so going to a restaurant on campus for lunch or exercising in the gym is the same as going anywhere else in the city.
Do you plan the children’s groups and preschools in cooperation with the municipality?
MŠ: The town hall helped us to find a private operator for the children's group we opened in Tachov for the public last autumn. We are once again negotiating with the town hall for the opening of the planned preschool. In fact, it is also one of the parties interested in operating it.
In Tachov, you also want to build a residential section by the campus. Is this part of the concept, or are you just taking advantage of the opportunity that the site offers for further development?
RH: It’s part of the complexity of our campuses. Thus, we’ll be creating dozens of start-up flats and the preschool. This is an opportunity for employers, for example, to provide their workers with affordable housing near their jobs as part of their employee benefits. In this way we are strengthening the insufficient social infrastructure for the town and the community.
Will they be rental flats that you will own and rent?
MŠ: Precisely. In addition, Tachov, just like the whole country, has long faced a lack of rental flats. There arren’t one- and two-room start-up flats being built there. Our rental flats will be available to the general public, and will not be intended solely for the needs of the companies and their staff on campus.
How did you choose the three locations you own?
RH: Bruntál and Tachov are regional centres with a tradition of production. We entered these locations through the acquisition of Alfa Plastik, a production company that was about to go bankrupt and both rather neglected complexes were a burden. The properties have been allocated so that the production company can concentrate on restructuring and developing its core business. Then we started to revitalise and develop both campuses. In this way, not only did we save the production company, but also both industrial sites.
Have you renovated the existing buildings or built all new ones?
RH: The renovation was comprehensive, from the infrastructure to the buildings. We preserved the original buildings, reconstructed the roofs, façades, structural elements, distribution systems and interiors. Plus, we managed to do it with the tenants in full operation. It was quite difficult to coordinate everything so that it wasn’t necessary to interrupt the clients’ precision production. In Tachov, you can no longer tell which buildings were built in the 70s and which are completely new.
Do the original buildings after reconstruction meet the energy efficiency parameters that tenants demand today?
RH: For the existing buildings, we’ve reduced energy consumption by more than 80 percent. This means significant savings for manufacturing companies, where energy and utilities comprise a significant cost item. This is also one of the reasons why the companies that worked in the original buildings have remained in them to this day. Even the original 50-year-old buildings are in the energy performance class A – extremely economical. Meanwhile, the achievement of such a classification is much more demanding than in a simple logistics hall.
Did you have to adapt the buildings specifically for the tenants because of the technologies used, or could any company come to them?
MŠ: For industrial buildings, market standards, such as the minimum height or span of columns, must be respected. But then there are the elements that we customise for our clients. We also supply them with solutions for internal distribution systems for the production technologies, which is atypical for each client. These costs are quite financially demanding. We’re able to distribute these one-time costs to the clients over the entire rental period.
RH: Production is always more sophisticated than logistics. You need to ensure a stable production environment for a wide range of production technologies. Some of them produce heat, some consume it. You need load floors, crane tracks, a greater proportion of daylight, larger facilities for employees. The energy management is more complex than in logistics halls.
What space do you have for further expansion in each location?
MŠ: In Tachov, we can build an additional 55 thousand square metres in three buildings for industrial production within six to nine months. At the same time, we’re looking for on operator for the multifunctional building with the prevailing service of hotel accommodation. In Bruntál, we have almost 60 thousand square metres available in four potential halls, which could be created during the next year. We are going in a different direction there than in Tachov. Three of these planned halls are smaller and more suitable in size for this region. Even a smaller company that needs only 3 to 5 thousand square metres, can have a separate hall there. In addition, in Bruntál we are able to deliver a hall with a net height of up to 20 metres. In Žirovnice we’re preparing a project on the order of 20 thousand square metres.
Do you already have building permits for these buildings?
RH: We already have a valid building permit in Tachov, so we could start building “tomorrow”. In Bruntál, we are in the final phase of the permit process for the construction of the entire campus.
Do you build only on order or do you also try speculative construction?
MŠ: We only build on order for specific clients, because we specialise in manufacturing, industrial companies. We want the hall to be customised for them.
How long do you conclude leases with the companies?
MŠ: We have a minimum of 10-year lease agreements. Since they are manufacturing companies, they want to have a stable environment and conditions, while any move would be very expensive for them. Of course, we also want them to stay with us for as long as possible. That gives us a greater incentive to make sure that the space suits them as much as possible.
Are you looking for new locations?
RH: We are actively looking for possible acquisitions. We have created a product that is also in demand in larger cities such as Prague, Brno and Ostrava. We are also looking for brownfields there, because they are already part of the cities and they make the most sense to us.
The industrial property sector is doing well in Czech Republic. The vacancy rate is practically zero. How do you see its future?
MŠ: The supply is still trying to catch up with demand. But we see that manufacturing companies are starting to choose and have requirements for sustainability, low energy intensity and energy self-sufficiency. That has been a big topic in the last two years.
RH: The trend of sustainability and ESG bring new demands on buildings and entire complexes. Manufacturing companies do not have the capacity nor generally the know-how to develop or reconstruct buildings, or to apply modern comprehensive energy solutions in them, they need to concentrate on their own activities. That’s an opportunity for us.
You are working quite a lot with energy self-sufficiency in Tachov, where you're planning a mix of different alternative energy sources. To what extent can such an industrial complex be energy self-sufficient?
RH: It’s certainly more demanding than logistics real estate. Automation and robotisation are spreading in production, and this requires more electrical power and higher capacities of other utilities. The advantage of our campuses is that they are historically dimensioned for industrial production. We are then trying to add more green energy solutions to existing capacities, so that tenants are less dependent on external energy supplies. We strive to cover consumption as much as possible through local resources, although one hundred percent self-sufficiency can hardly be achieved in production complexes.
What do the specific figures look like in Tachov
RH: We are now building a solar power plant with an annual production of 5 gigawatt hours, one of the largest in the Czech Republic. That will be able to cover about 50 percent of the annual energy consumption in the production plants. We are also analysing the potential of wind energy. We want to install smaller wind turbines in the campuses, either on the roofs or in the gaps between the buildings. Altogether, we could cover more than 60 percent of the annual electricity consumption on the campus. We’re installing a high-capacity battery storage system, which will also be connected, among other things, to charging stations for electric vehicles.
Are you also building your own sources of heat or drinking water?
RH: We're installing heat pumps that use geothermal energy. For water, we should be able to achieve 100% self-sufficiency thanks to our own deep wells for drinking water. We collect and reuse rainwater. We have measures to ensure that it is also absorbed as much as possible directly in the complex and does not leak into the sewage treatment plant. We are also resolving the use of grey water. Thus, we are covering the entire spectrum.
MŠ: We have our own Urbanity Energy division, which deals with the energy infrastructure and energy management in our campuses. We can supply tenants with energy from local renewable sources, so we help them fulfil their sustainability commitments. From this perspective, we see energy as a strategically important part of our business.
The Tachov campus has been awarded the international BREEAM Communities certificate. What does the certification consist of?
RH: The Tachov Campus was the first in the Czech Republic to achieve it and the first in the world as a predominantly industrial complex. City districts, which combine public space with office and residential buildings, are usually certified because of the need to meet the strict criteria of this certificate.
What did you have to fulfil to get it?
MŠ: One of the conditions is that you communicate with the public about the project and include its suggestions. You also need to take care of the aesthetic aspect. You have to prove that you are not burdening the location, but rather developing it. A great emphasis is placed on ecology, for example water management and the placement of solar power plants on otherwise hard-to-use areas. During construction, you should recycle the original raw materials, use local suppliers.
Does the certificate help you in dealing with potential tenants?
RH: The comprehensive certificate demonstrates the high quality and sustainability of our campuses to potential tenants. That we focus not only on the buildings themselves, but on broader relationships, on provided services that go beyond the norm and on close links with the city. They know that they have an opportunity to become part of a locality that is in tune with the local community and does not create any social or other tensions, that they can simply become a good and considerate neighbour from the very beginning.
Roland Hofman
He is the co-founder of Urbanity Group, acting as the CEO. In the past, he held senior managerial and statutory positions
in companies belonging to the investment company M.L Moran (e.g., KPŽ, Technistone and Thermolast). He has been associated
with M.L. Moran since 2001, and also serves as the Chairman of the Supervisory Board here. After studying at VŠB-TU Ostrava,
he gained experience with top management in London, where he also earned an MBA from the University of Greenwich. He has
long specialised in the investment, management and development of commercial real estate.
Markéta Šimáčková
She works as the COO in Urbanity and is also responsible for Business Development. She graduated from the University of Economics in Prague, where she also studied for an MBA with a focus on commercial real estate and their valuation. She worked as the General Manager and Executive Director of the TORINO-PRAGA Invest real estate group. She also has experience from the international company Cushman & Wakefield.
Author: Jan Stuchlík